AIMPLAS, Instituto Tecnológico del Plástico, ha completado el proyecto europeo BRIGIT tras 48 meses de investigaciones. En él han participado otros 15 socios entre los que se encuentran la Universidad de Cantabria y la empresa española Green Source S.A. Gracias a estas investigaciones se ha obtenido como resultado una nueva generación de paneles ignífugos para el interior de camiones y autobuses fabricados a partir de biopolímeros procedentes de subproductos de la fabricación de pasta de celulosa papelera.
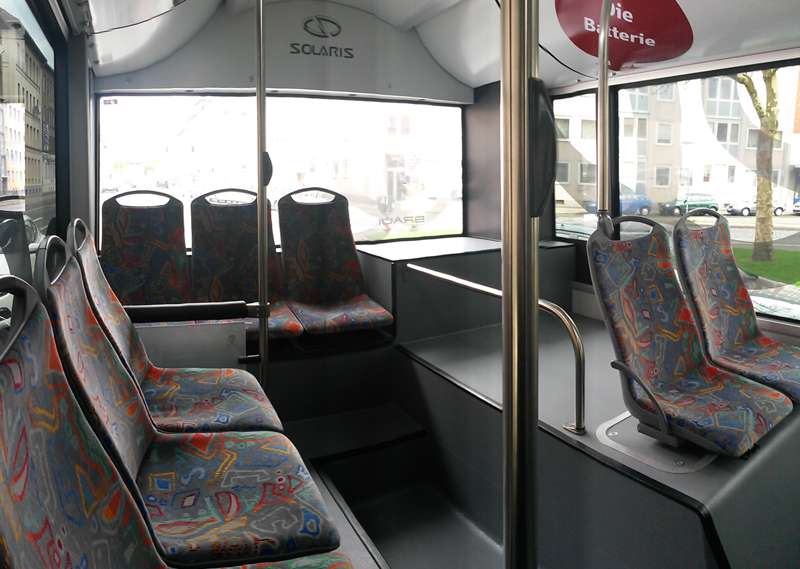
El proyecto BRIGIT, que arrancó en agosto de 2012, ha contado con la financiación de fondos europeos dentro del VII Programa Marco bajo el número de acuerdo KBBE-2012-6-311935. Durante su realización, se ha abordado desde la obtención de los biopolímeros, su formulación y modificación para mejorar su comportamiento al fuego hasta el procesado de los biocomposites resultantes para la posterior fabricación de los paneles que se instalarán en el interior de los camiones y los autobuses de Solaris y Fiat. Además, se ha validado la viabilidad económica y medioambiental de los nuevos productos.
Alto valor añadido para los residuos de la fabricación de celulosa
Para lograr los innovadores paneles, los socios del proyecto han desarrollado un nuevo proceso de obtención de los bioplásticos, concretamente PHB (polihidroxibutirato) y PBS (polibutileno succinato), más ecológico que los existentes, a partir de subproductos del proceso de obtención de la celulosa. Como explica el investigador principal del proyecto Miguel Ángel Valera: “el empleo de los subproductos del proceso de producción de la celulosa como fuente de azúcares necesarios para realizar el proceso de fermentación de los microorganismos que producen el PHB y el ácido succinico, permite una integración de los procesos necesarios para la obtención de los biopolímeros empleados en BRIGIT y por lo tanto un ahorro en los costes de producción”.
Vehículos más reciclables y ecológicos
Mediante técnicas de compounding, AIMPLAS se ha encargado de mezclar y modificar ambos biopolímeros para obtener un biocompuesto con altos requerimientos. En primer lugar, se trata de un material procesable mediante extrusión, con la resistencia mecánica y al fuego que exige la industria del transporte, pero con la ventaja añadida de ser totalmente biodegradable y también compostable tras su triturado a diferencia de las
resinas termoestables que se utilizan actualmente.
Posteriormente, y mediante moldeo por compresión continua, se han fabricado los paneles multicapa formados por láminas de biocompuesto y fibras naturales (en sustitución de la habitual fibra de vidrio), y un núcleo ligero de corcho en su interior. Además de instalarse en el interior de camiones y autobuses en forma de columnas y paneles laterales, estos paneles 3D se podrán aplicar también en trenes, barcos, furgonetas y otros medios de transporte de mercancías y personas.